Last fall, Glenn H. Fredrickson, professor of chemical engineering, received the Materials Theory Award at the fall 2017 meeting of the Materials Research Society. The award, which honors Fredrickson for “pioneering the development of field-theoretic computer simulation methods and their application to investigate and design self-assembling polymers and soft materials,” came a year after he received the American Institute of Chemical Engineers William H. Walker Award for Excellence in Contributions to Chemical Engineering Literature.
“We’re trying to develop new ways of simulating soft materials — complex materials composed of polymers and other ingredients, which can be applied in developing new types of plastics as well as consumer products,” Fredrickson says in a video interview about his research.
“This award recognizes Glenn Fredrickson’s immense and impactful contributions to theory and simulation of polymer self-assembly,” said Rachel Segalman, the Edward Noble Kramer Professor and chair of UCSB’s Department of Chemical Engineering. “Many of the methods Glenn has developed are now widely used both in academia and in industrial systems. We are incredibly proud of his achievements.”
For the most part, polymers and soft materials are developed by trial and error, Fredrickson explains. “People modify the chemical structure of the building blocks and the monomers that make up the polymers. There are multiple components, and how they all interact to establish material properties is generally determined in an Edisonian trial-and-error kind of way.”
Around 2000, he recalls, “We had the dream that we could build computer models for how all these components interact, and then run some sort of simulation to see how the material would structure and what its properties might be. And the system would require a feedback loop so that multiple computers could be grinding away trying to determine an optimal recipe.”
Over the past fifteen years, Fredrickson and his collaborators have realized that dream — and received widespread recognition for their revolutionary accomplishments — by developing a method that enables rapid simulations of highly complex polymer systems, thus vastly expanding the number of materials “recipes” that can be tried.
The old process for predicting the properties of a long macromolecule — i.e. a polymer — involved specifying how little bits that represent the building blocks of one polymer interact with the little bits that make up the other polymers in a material system, with the bits’ relative spatial proximity assigned to an interaction potential. In a computer simulation, the little bits are treated as classical particles that experience the force field created by the interactions with the other particles. “You solve Newtonian mechanics, F = MA [force = mass x acceleration], to evolve the particles’ positions over time and then see how things assemble,” Fredrickson explains.
The challenge in simulating polymers that are of practical interest as materials is that they are usually very large macromolecules. When they are melted together, their entangled chains resemble spaghetti, and because they are so entangled, they move very slowly. “It’s easy to do a molecular simulation of a small, relatively simple molecule like water, but when you have a highly concentrated assembly of polymers, the constituent parts barely move, and you end up being limited by the time scale of the simulation you can run. In most cases, even with massive computer resources, it is not possible to run simulations long enough to bring such a system to an equilibrium state in which the material structure is established and properties don’t change.” Fredrickson says.
Fredrickson’s lab came up with a revolutionary alternative to that procedure. “We follow a similar process, but we don't work with particle coordinates. Rather, we convert the interacting particle models into mathematically equivalent models involving fields, i.e. continuous functions defined over the same spatial domain as the particles. The particle coordinates are then eliminated, but the fields remain and interact with each other in an equivalent “field theory” model. Computer simulations of these field theories allow us to access material structures that are much larger than what can be modeled using traditional particle-based approaches, and also makes it possible to equilibrate systems that could not be brought to equilibrium otherwise.”
The relevant mathematical techniques Fredrickson employs for converting what is called a “many-body problem,” involving a collection of interacting atoms, molecules, or, in this case, polymers, into what' is called a “statistical field theory” have been known for at least sixty years, but they have never been the basis for trying to do more than paper-and-pencil calculations.
“Once we have transformed the many-polymer model into a field theory, then we project the fields onto a discrete grid in a computational domain and then evolve those field variables through time to conduct a numerical simulation,” he says. “So while the simulation is based on the field variables, not on the polymer coordinates, all the specifics of the molecules’ chemical structure, architecture, size, and interactions are embedded in the field theories. This approach allows us to equilibrate even very dense polymer systems that have high molecular weight and are structured on length scales ranging from nanometers to microns. With that ability, we can pursue a vast range of applications.”
This “field-theoretic simulation” (FTS) approach is significant not only for its fundamental importance to polymer science and molecular thermodynamics, but also for its engineering impact on directed self-assembly, an emerging lithographic technique for patterning semiconductor devices. Companies such as Intel and Samsung are developing next-generation lithographic processes based on FTS software tools developed by the Fredrickson group at UCSB.
As digital circuits become ever smaller, companies that are designing the next generation of micro-electronic devices — both microprocessors and storage devices — are approaching the scaling limits of lithography, the optical process used to pattern circuits onto chips. Thus, they have become interested in using self-assembling polymer molecules, like block copolymers, to spontaneously form fine patterns on a length scale of about 10 nanometers (nm), which can then be transferred to silicon substrates and used to fabricate the circuits.
“The industry challenge is to move to a finer and finer scale,” Fredrickson says. “They use short-wavelength 193nm light in a photoresist system to do the patterning, and they invoke every optical physics trick in the book to get as fine as they can.”
As an example, he explains, “Say you want to put a conductive wire from one layer of the chip to the next. Usually, that is done using 193-nm light focused on a photoresist layer to create a cylindrical cavity, which is then etched into the substrate and back-filled with metal to create a vertical interconnect access, or VIA.
“But with current lithography, the narrowest you can make that cylindrical hole, with good fidelity, is about 50 nm in diameter, while you would ideally like it to be narrower, say 10 nm across." He explains that a workaround for making things like VIAs is to create the same guiding 50-nm cavity in photoresist, but then to pour a solution of block copolymer into it and use heat to dry and anneal it. If the block polymer is designed properly, it will self-assemble a narrow 10-nm-diameter cylinder composed of one of the block segments centered within the bigger cylinder. The small cylinder is chemically different from its surroundings, so it can be selectively etched into the substrate of the silicon wafer, creating a precise narrow hole that can later be filled with metal to create a VIA.
This process, called “directed self-assembly” (DSA) — because it combines top-down lithography with bottom-up molecular self-assembly — allows molecules to assemble spontaneously as they would across a polymer film or in a bulk material, but assembly occurs in tight confinement guided by the top-down optical lithography tool.
Fredrickson notes that one of the biggest challenges in this work is avoiding defects, which need to be reduced to the parts-per-billion level. “This is an industry that doesn’t like defects, and self-assembling soft materials are intrinsically defective,” he says. “So, with our corporate partners, we have exploited the FTS modeling tools to better understand the types of defects that occur and to help them design DSA processes that minimize defect formation.”
The honors and awards continue to roll in, recognizing Fredrickson and his lab for their groundbreaking work, which plays a critical role in developing new polymers to support the ongoing micro-electronics revolution.
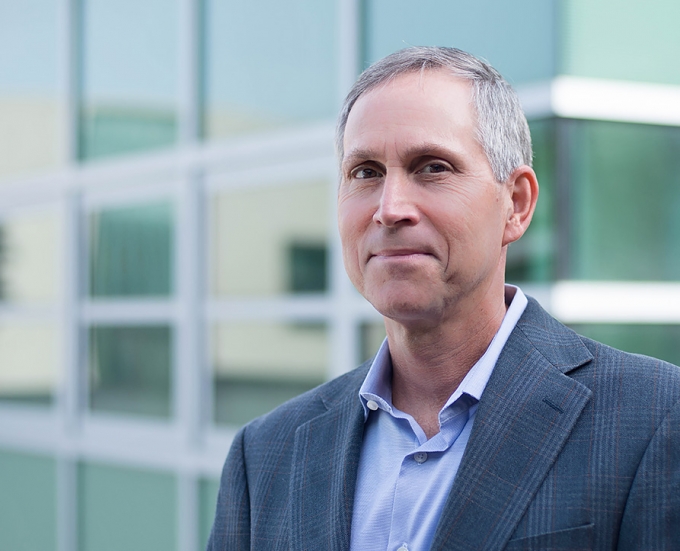
Professor Glenn H. Fredrickson outside his office in the Materials Research Laboratory building. Photograph by Ryder Rogers